CNC Lathe Parts Factories: Driving Precision in Metal Fabrication
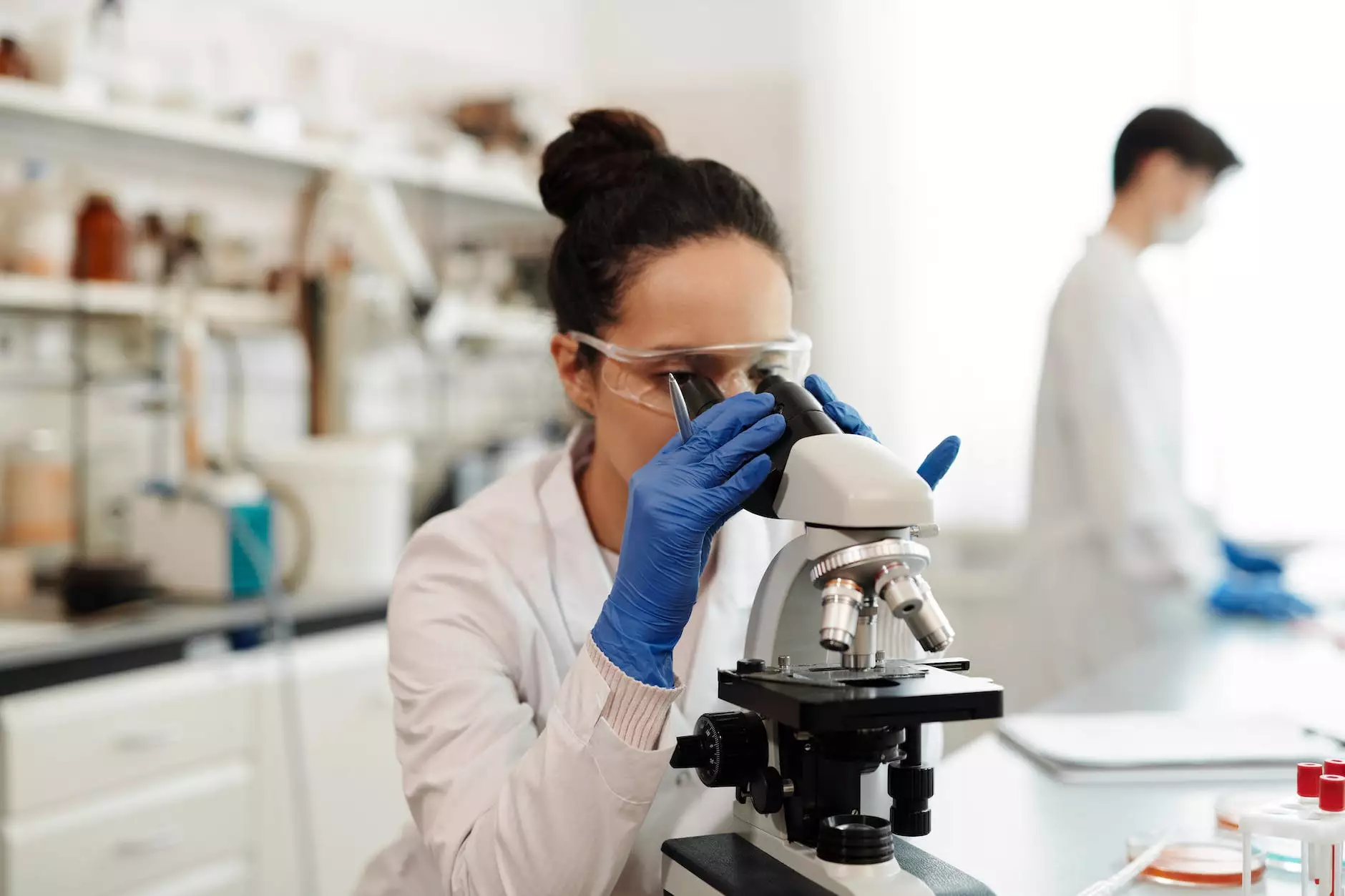
The manufacturing industry is constantly evolving, with technology playing a pivotal role in shaping its future. Among the innovations that have significantly impacted metal fabrication are CNC lathe parts factories. These facilities leverage advanced computer numerical control (CNC) technology to produce intricate parts with unmatched precision and efficiency. In this article, we will delve into the workings of CNC lathe parts factories, their significance in the metal fabrication realm, and how they contribute to the success of businesses like deepmould.net.
Understanding CNC Technology
Before we can fully appreciate the impact of CNC lathe parts factories, it's essential to understand what CNC technology entails. CNC, or Computer Numerical Control, refers to the automated control of machining tools by means of a computer. This technology allows for the precise cutting, drilling, and milling of materials such as metal, plastic, and wood, making it a cornerstone of modern manufacturing.
The Evolution of CNC Technology
The origins of CNC technology date back to the 1950s when it was used primarily for large manufacturing processes. The transition from manual to computer-controlled systems marked a significant leap in production capabilities. Over the decades, advancements in software and hardware have allowed CNC machines to become more sophisticated, enabling manufacturers to produce parts that were previously deemed impossible.
The Role of CNC Lathe Parts Factories
CNC lathe parts factories specialize in manufacturing components that require rotational symmetry. The lathe, a critical machine tool in these factories, spins a workpiece against cutting tools to shape it into the desired form. This process is enormously beneficial for creating components like shafts, bushings, and spindles, widely used across various industries. Here’s why these factories are indispensable:
1. Precision and Accuracy
One of the foremost advantages of CNC lathe parts factories is their ability to produce parts with exceptional precision. Traditional machining methods often result in variances that can lead to subpar products. In contrast, CNC technology eliminates human error, ensuring that every part manufactured is consistent and accurate. This is crucial for industries such as aerospace, automotive, and medical, where even the smallest discrepancy can have catastrophic consequences.
2. Increased Efficiency
Efficiency is a key metric in manufacturing. CNC lathe parts factories can operate continuously, significantly reducing production time. A single CNC machine can perform multiple operations without the need for manual intervention, leading to a dramatic increase in output. This efficiency not only reduces labor costs but also allows companies to meet tight deadlines without compromising quality.
3. Cost-Effectiveness
While the initial investment in CNC technology may be substantial, the long-term savings are undeniable. By automating the manufacturing process, CNC lathe parts factories can help businesses reduce waste and lower labor costs. Furthermore, the precision of CNC machining minimizes material waste, leading to more cost-effective operations overall.
Applications of CNC Lathe Parts Factories
CNC lathe parts factories serve a myriad of industries, providing specialized components that cater to specific needs. Below are some key sectors that benefit from these factories:
Aerospace Industry
The aerospace sector demands the highest standards of precision and reliability. CNC lathe parts factories produce critical components such as engine parts and landing gear mechanisms. The ability to manufacture parts that meet stringent safety regulations is paramount, and CNC technology meets these challenges head-on.
Automotive Industry
The automotive industry requires a vast array of components, from engine blocks to transmission housings. CNC lathe parts factories play an integral role in producing high-quality parts that contribute to vehicle performance and safety. The efficiency of CNC machining ensures that manufacturers can keep pace with demand while maintaining stringent quality standards.
Medical Equipment Manufacturing
In the medical field, precision is not just preferred; it is essential. CNC lathe parts factories produce components for surgical instruments and medical devices, where accuracy can determine patient outcomes. The ability to create custom parts tailored to specific medical applications is a unique advantage that enhances the efficacy of healthcare devices.
Electronics Manufacturing
The electronics industry also relies on CNC lathe parts factories for producing intricate components like connectors and housings. With the rapid advancement of technology, these factories are equipped to handle the fast-paced demands of electronic manufacturing, producing high-quality parts with quick turnaround times.
The Process of CNC Machining in Lathe Parts Factories
The CNC machining process in lathe parts factories is streamlined and highly efficient. Below are the fundamental steps involved in this process:
1. Design Phase
The first step in CNC machining is designing the component using CAD (Computer-Aided Design) software. Engineers create a detailed model of the part, specifying dimensions and tolerances. This digital representation serves as the blueprint for the machining process.
2. Programming
Once the design is finalized, it is converted into a program that the CNC machine can understand. This involves creating a series of instructions that dictate how the machine will move, what tools it will use, and the sequence of operations.
3. Setup
Before machining can commence, the operator sets up the CNC lathe by installing the workpiece and configuring the necessary tools. Proper setup is critical for ensuring precision and minimizing the risk of errors during production.
4. Machining
During the machining phase, the CNC lathe takes over. The machine follows the programmed instructions to shape the part. It can perform various operations like turning, drilling, or milling, depending on the design specifications.
5. Quality Control
After machining, parts undergo rigorous quality control inspections. Advanced measuring tools are used to verify that the dimensions and tolerances fall within acceptable limits, ensuring that every component meets industry standards.
The Future of CNC Lathe Parts Factories
As technology continues to advance, the future of CNC lathe parts factories looks promising. Several trends stand out that are likely to shape the industry:
1. Integration of AI and Machine Learning
The introduction of Artificial Intelligence (AI) and Machine Learning in CNC machining is set to revolutionize operations. These technologies can analyze data in real time, allowing for predictive maintenance, tailored production schedules, and enhanced efficiency.
2. Increased Automation
Automation will play a critical role in the evolution of CNC lathe parts factories. With robots and automated systems taking on more tasks, these factories can operate efficiently 24/7, further reducing costs and improving output.
3. Sustainable Practices
As environmental consciousness rises, CNC lathe parts factories will increasingly focus on sustainable practices. This includes minimizing waste, using eco-friendly materials, and optimizing energy consumption, aligning with global efforts toward sustainable manufacturing.
Conclusion
CNC lathe parts factories are at the forefront of the metal fabrication industry, driving innovation and precision. Their ability to produce high-quality, efficient components is irreplaceable across numerous sectors, from aerospace to medical manufacturing. Businesses like deepmould.net are prime examples of how embracing CNC technology can lead to significant advancements in production quality and operational efficiency. As we look to the future, the integration of AI, increased automation, and sustainable practices will undoubtedly further enhance the capabilities of CNC lathe parts factories, solidifying their crucial role in modern manufacturing.
FAQs About CNC Lathe Parts Factories
What are the primary benefits of using CNC lathe parts factories?
The primary benefits include precision, efficiency, and cost-effectiveness in producing high-quality components for various industries.
How does the CNC machining process work?
The CNC machining process involves design, programming, setup, machining, and quality control, all aimed at creating precise components.
What industries primarily use CNC lathe parts?
CNC lathe parts are used across a variety of industries, including aerospace, automotive, medical, and electronics manufacturing.